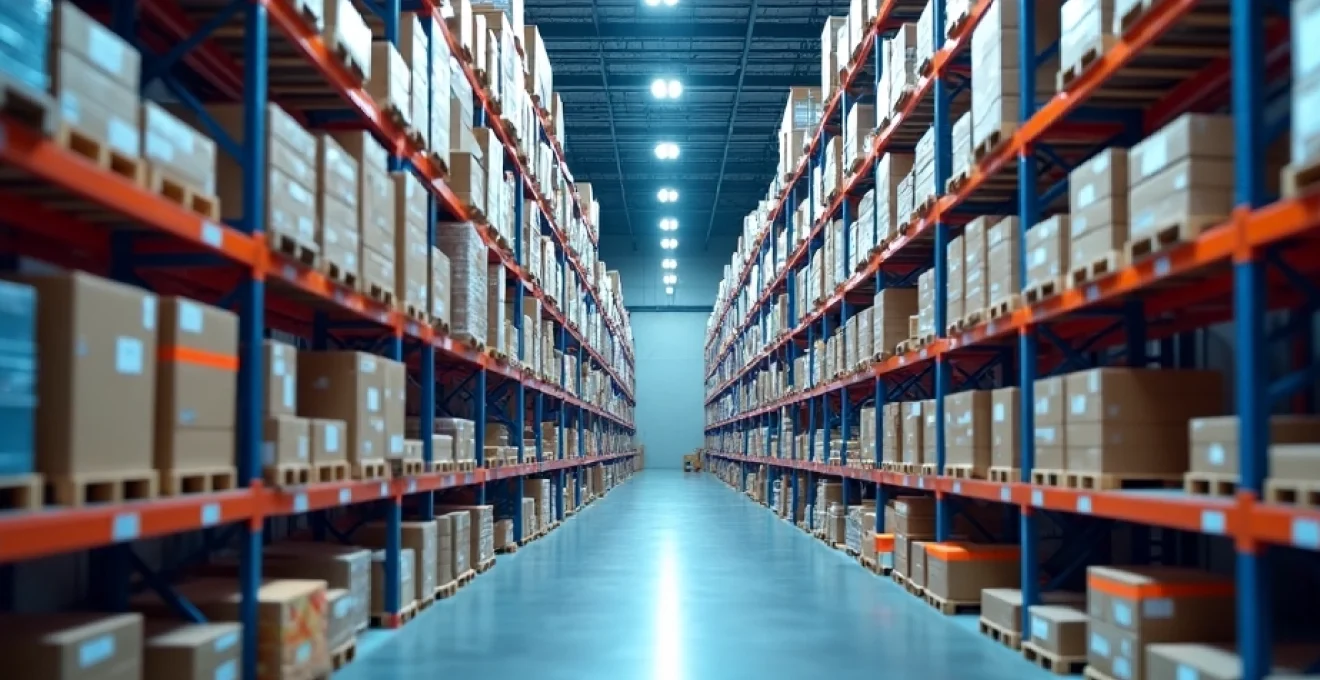
La gestión eficiente de almacenes es un pilar fundamental para el éxito de cualquier cadena de suministro moderna. En un entorno empresarial cada vez más competitivo, optimizar las operaciones de almacenamiento no solo reduce costos, sino que también mejora la satisfacción del cliente y aumenta la ventaja competitiva. La implementación de tecnologías avanzadas, estrategias de diseño inteligentes y métodos de gestión de inventario innovadores son esenciales para mantenerse a la vanguardia en la industria logística actual.
Sistemas de gestión de almacenes (WMS) avanzados
Los sistemas de gestión de almacenes (WMS) avanzados son la columna vertebral de las operaciones logísticas modernas. Estos sistemas proporcionan una visibilidad en tiempo real del inventario, optimizan los procesos de picking y mejoran la precisión general del almacén. La elección del WMS adecuado puede transformar radicalmente la eficiencia de su almacén.
Implementación de SAP Extended Warehouse Management
SAP Extended Warehouse Management (EWM) es una solución robusta que ofrece capacidades avanzadas para gestionar operaciones de almacén complejas. Con SAP EWM, usted puede optimizar los flujos de trabajo, mejorar la utilización del espacio y aumentar la productividad de los empleados. Este sistema se integra perfectamente con otros módulos de SAP, proporcionando una visión holística de su cadena de suministro.
Optimización con oracle warehouse Management Cloud
Oracle Warehouse Management Cloud es una solución basada en la nube que ofrece flexibilidad y escalabilidad para operaciones de almacén de todos los tamaños. Con sus capacidades de inteligencia artificial y aprendizaje automático, usted puede predecir y optimizar los patrones de demanda, mejorar la precisión del inventario y reducir los tiempos de ciclo de los pedidos.
Integración de Manhattan SCALE para operaciones complejas
Manhattan SCALE es una solución WMS altamente configurable diseñada para operaciones de almacén complejas. Ofrece funcionalidades avanzadas como gestión de trabajo por olas, optimización de rutas de picking y gestión de transportistas. Al implementar Manhattan SCALE, usted puede mejorar significativamente la eficiencia operativa y la precisión del cumplimiento de pedidos.
Tecnologías de automatización en almacenes
La automatización es la clave para llevar la eficiencia del almacén al siguiente nivel. Las tecnologías de automatización no solo reducen los errores humanos, sino que también aumentan la velocidad y precisión de las operaciones. La implementación estratégica de estas tecnologías puede resultar en mejoras dramáticas en la productividad y la rentabilidad.
Sistemas de clasificación automática (sorters) de interroll
Los sistemas de clasificación automática de Interroll son soluciones de alta velocidad que pueden manejar una amplia gama de productos. Estos sistemas utilizan tecnología de clasificación cruzada para distribuir eficientemente los artículos a sus destinos correctos dentro del almacén. Al implementar los sorters de Interroll, usted puede aumentar significativamente la velocidad de procesamiento de pedidos y reducir los errores de clasificación.
Robots móviles autónomos (AMR) de fetch robotics
Los robots móviles autónomos (AMR) de Fetch Robotics representan el futuro de la manipulación de materiales en almacenes. Estos robots pueden navegar de forma independiente por el almacén, transportando productos y realizando tareas de picking. La implementación de AMR puede reducir drásticamente los tiempos de desplazamiento de los trabajadores y mejorar la eficiencia general del almacén.
Soluciones de almacenamiento vertical kardex remstar
Las soluciones de almacenamiento vertical de Kardex Remstar son ideales para maximizar el espacio de almacenamiento en instalaciones con limitaciones de superficie. Estos sistemas utilizan el espacio vertical disponible, permitiendo almacenar más productos en una huella más pequeña. Además, mejoran la ergonomía y la seguridad para los trabajadores al traer los productos al nivel del operador.
Sistemas de transporte automatizado (AGV) de elettric80
Los sistemas de transporte automatizado (AGV) de Elettric80 ofrecen una solución flexible y eficiente para el movimiento de materiales dentro del almacén. Estos vehículos pueden transportar pallets y cargas pesadas de forma autónoma, reduciendo la necesidad de intervención humana y minimizando los riesgos de accidentes. La implementación de AGV puede optimizar los flujos de trabajo y mejorar la seguridad en el almacén.
La automatización en los almacenes no es solo una tendencia, sino una necesidad para mantenerse competitivo en el mercado actual. Las empresas que adoptan estas tecnologías ven mejoras significativas en eficiencia y precisión.
Estrategias de diseño y layout de almacenes
El diseño y layout de un almacén son fundamentales para su eficiencia operativa. Un diseño bien planificado puede reducir los tiempos de desplazamiento, optimizar el flujo de materiales y mejorar la utilización del espacio. La implementación de estrategias de diseño inteligentes puede tener un impacto significativo en la productividad general del almacén.
Metodología lean warehouse para optimización de espacios
La metodología Lean Warehouse se centra en eliminar el desperdicio y optimizar los procesos en el almacén. Esta metodología implica la identificación y eliminación de actividades que no agregan valor, la estandarización de procesos y la mejora continua. Al aplicar los principios Lean, usted puede mejorar la eficiencia del flujo de materiales y reducir los costos operativos.
Análisis de flujos con diagramas de espagueti
Los diagramas de espagueti son una herramienta visual poderosa para analizar y optimizar los patrones de movimiento dentro del almacén. Estos diagramas trazan las rutas de los trabajadores y los materiales, permitiendo identificar ineficiencias y áreas de congestión. Al utilizar diagramas de espagueti, usted puede rediseñar el layout del almacén para minimizar los desplazamientos innecesarios y mejorar el flujo de trabajo.
Implementación de zonas de picking dinámicas
Las zonas de picking dinámicas son áreas flexibles que se pueden ajustar según las necesidades cambiantes del inventario y los patrones de demanda. Estas zonas permiten una mayor eficiencia en la preparación de pedidos al colocar los productos de alta rotación en ubicaciones de fácil acceso. La implementación de zonas de picking dinámicas puede reducir significativamente los tiempos de picking y mejorar la productividad general del almacén.
Gestión de inventarios y técnicas de reposición
Una gestión de inventarios eficiente es crucial para mantener un equilibrio entre la disponibilidad de productos y los costos de almacenamiento. Las técnicas de reposición adecuadas pueden ayudar a reducir el exceso de inventario, minimizar los costos de mantenimiento y mejorar el flujo de caja de la empresa.
Método ABC de clasificación de inventarios
El método ABC de clasificación de inventarios es una técnica que categoriza los productos según su importancia en términos de valor y frecuencia de uso. Los artículos "A" son los más valiosos y requieren un control más estricto, mientras que los artículos "C" son menos críticos. Al implementar esta clasificación, usted puede asignar recursos de manera más eficiente y optimizar las estrategias de almacenamiento y reposición.
Sistema kanban para reposición Just-In-Time
El sistema Kanban es una técnica de reposición visual que se utiliza para implementar el principio Just-In-Time (JIT) en el almacén. Este sistema utiliza tarjetas o señales visuales para indicar cuándo es necesario reponer un producto. Al implementar Kanban, usted puede reducir el exceso de inventario, minimizar los tiempos de espera y mejorar el flujo de materiales en el almacén.
Técnicas de cross-docking para reducción de almacenamiento
El cross-docking es una estrategia logística que minimiza el tiempo de almacenamiento al transferir los productos directamente desde la recepción a la expedición. Esta técnica es especialmente útil para productos de alta rotación o pedidos urgentes. Al implementar el cross-docking, usted puede reducir los costos de almacenamiento, acelerar el tiempo de entrega y mejorar la satisfacción del cliente.
La gestión eficiente del inventario no solo reduce costos, sino que también mejora la capacidad de respuesta a las demandas del cliente. Las empresas que dominan estas técnicas logran una ventaja competitiva significativa en el mercado.
Métricas y KPIs para la eficiencia en almacenes
Para mejorar la eficiencia en la gestión de almacenes, es esencial medir y monitorear el rendimiento de manera constante. Las métricas y KPIs (Indicadores Clave de Rendimiento) proporcionan una visión objetiva del desempeño del almacén y ayudan a identificar áreas de mejora. A continuación, se presentan algunos de los KPIs más importantes para evaluar la eficiencia en almacenes.
Tasa de precisión de inventario (inventory accuracy rate)
La tasa de precisión de inventario mide la exactitud entre el inventario físico y los registros del sistema. Una alta precisión de inventario es crucial para evitar problemas como agotamientos de stock o exceso de inventario. Para calcular este KPI, usted puede usar la siguiente fórmula:
Tasa de precisión de inventario = (Número de ubicaciones correctas / Total de ubicaciones contadas) x 100
Una tasa de precisión de inventario del 95% o superior se considera generalmente aceptable en la industria.
Tiempo de ciclo de pedido (order cycle time)
El tiempo de ciclo de pedido mide el tiempo transcurrido desde que se recibe un pedido hasta que se envía al cliente. Este KPI es crucial para evaluar la eficiencia general del almacén y la satisfacción del cliente. Para mejorar este indicador, usted puede optimizar los procesos de picking, embalaje y expedición.
Un tiempo de ciclo de pedido típico puede variar según la industria, pero en general, cuanto más corto sea, mejor será la percepción del cliente sobre la eficiencia de su servicio.
Productividad de picking (pick productivity)
La productividad de picking mide la eficiencia de los operarios en la preparación de pedidos. Este KPI se calcula generalmente como el número de líneas de pedido preparadas por hora de trabajo. Para mejorar la productividad de picking, usted puede implementar tecnologías como el picking por voz o sistemas de pick-to-light.
Productividad de picking = Número de líneas preparadas / Horas de trabajo
La productividad de picking puede variar significativamente según el tipo de productos y el diseño del almacén, pero es un indicador clave para medir la eficiencia operativa.
Utilización de espacio de almacenamiento (storage space utilization)
La utilización de espacio de almacenamiento mide qué tan eficientemente se está utilizando el espacio disponible en el almacén. Este KPI es crucial para optimizar los costos de almacenamiento y determinar si se necesita expandir o reorganizar el espacio. Para calcular este indicador, usted puede usar la siguiente fórmula:
Utilización de espacio = (Espacio ocupado / Espacio total disponible) x 100
Una utilización de espacio óptima generalmente se sitúa entre el 75% y el 85%. Una utilización por debajo del 75% podría indicar un exceso de capacidad, mientras que una utilización por encima del 85% podría resultar en congestión y reducción de la eficiencia operativa.